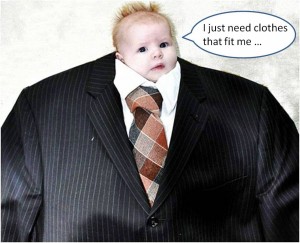
Less is more is a concept that is generally lacking in the field of engineering where the design philosophy seems often to make things more complex than they need to be.
I was reminded of this during a recent project for an oil refining client in the Middle East. It was the design of a piping system at the bottom of a column for transferring a stream through a series of heat exchangers into a downstream furnace. By well- established convention, the system would be designed for the highest possible flow rate and pressure drop of the system, with an allowance of an additional 30% of the total pressure drop for the control valve. This sets the pump (usually a centrifugal pump) differential pressure requirement.
If the pump was selected according to the commonly used API 610 standard, it would have to develop the differential pressure with an impeller diameter of 90% of maximum – to allow for possible future debottlenecking. The pump manufacturer would then offer the next frame size up in his range. All of this additional “up-sizing” would pile on the inefficiencies.
Now consider what this system will do when running at typical operating conditions – lower than maximum flow, less than design fouling, lower than design pressure requirement. The control valve balances the system by dissipating excess pumping pressure – it wastes energy.
If the control systems on your car worked like this you would start the engine, put your foot hard on the accelerator, let in the clutch and control the speed with the brake – a recipe for low efficiency and a smell of burning brake linings!
It is far better to control a hydrocarbon system by varying the energy input (the accelerator) by varying the speed of the driver. Do this with a variable speed electric motor or varying the speed of a steam turbine driver.
In this example, using a variable speed electric motor would save the plant more than US$ 200,000 less in energy per year – with an equivalent reduction in CO2 emissions.
Obviously in design engineering you need to factor in safety, robustness and functionality. But, when you look at the whole process from design to construction, each stage will add another factor of allowance in the name of safety. The result is a product that is over capacity and over complicated.
When a product is over-engineered, it becomes more expensive and wasteful because more capital and materials are required.
So, what’s the solution? Design engineers need to be smarter in the way they apply industry best practice procedures. Instead of following them to the letter, they should take a step back and consider what is actually required to make sure that the product they are designing achieves the desired performance.
In other words, a design that is fit for purpose.